Here are 8 common mistakes we find in pallet rack warehousing applications:
#1 Under Engineering Pallet Rack System
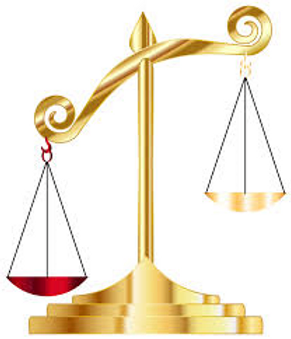
Understanding true weights / future weights of product
It is common for clients to underestimate the actual weight of pallets being stored in pallet rack. Pallet heights also have a significant factor in properly engineering a pallet rack system. The greater vertical distance between beams levels, the greater the upright capacity will need to be down rated. Formal data with pallet weights, pallet height/width/depth are important metrics to prevent under engineering.
In addition, under engineering wire decks is common and over time results in a wire deck with permanent deflection between channel supports that make the deck appear to have a “wave” like effect. Wire decks capacities are designed based on a uniform distributed load (UDL)
#2 Failure to Forecast Future Growth
Future growth should be considered when engineering a pallet rack system. This could relate to an increased weight of product going onto beam levels, or taller pallets requiring beam heights to change. Future growth can also be accomplished by adding beam levels, and if applicable, extending the height of uprights using a column splice / upright extension. Pallet rack can also be re-configured into higher density storage.
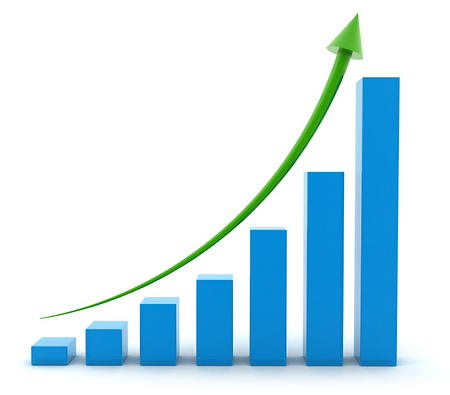
Addressing these scenarios in the preliminary design phase allows for potential changes to be pre-engineered into the system.
#3 Inadequate Sprinkler System
The sprinkler system in the warehouse will have a significant factor on how high and what types of commodities can be stored. It is important to know how your insurance provider classifies the commodities that will be stored in the pallet rack.
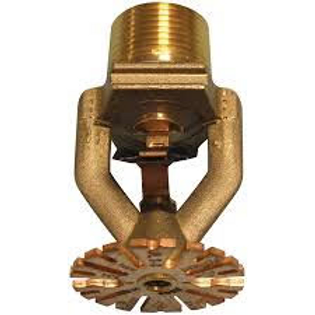
Commodities are most commonly classified as “Class I – IV” and “Group A – C Plastics”
If the building is not equipped with an ESFR (Early Suppression Fast Response) sprinkler system and the commodities are higher up on the hazardous/flammable scale, a sprinkler system modification or in-rack sprinklers may be required. In-rack sprinklers can still be required with an ESFR sprinkler system depending on the commodities/height of storage.
#4 Fall Protection of Pallets
A corporate culture committed to safety has been significantly shown to improve employee moral. Storing pallets on beams without fall safe support is not recommended. One accident is all it takes to more than justify the investment. Wire decks are the ideal solution for pallet fall-safe prevention. Pallet supports (snap-in, bolt-on, etc.) are also viable solutions.
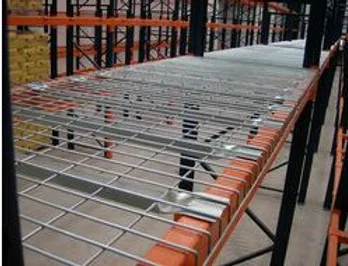
#5 Incorrect / Inefficient Slotting
In an order fulfillment application, a velocity slotting map identifying “through put” of product mix helps determine how the warehouse storage should be slotted to achieve optimal efficiency. As the product flow changes, re-slotting will take place to maintain peak performance. We find some clients don’t have a planned slotting schedule, and in many cases do not have a formal plan in place for identifying and adjusting product slotting in the warehouse.
#6 Pallet Height Variance (Dead Space)
In applications where pallet heights vary significantly, optimizing pallet storage requires accounting for various pallet heights. For example, a 6′ vertical beam to beam clearance does not optimize the storage of a 3′ tall pallet. In larger scale, these types of inefficiencies when properly addressed add up to significantly increased space utilization.
#7 Permitting
A High Piled Storage Permit is required when a building or portion thereof intends to store commodities in excess of 12 ft. for an area greater than 500 sq. ft., as dictated by Section 105.6.22, Chapter 23, or when required by the Fire Marshal.
If your company has relocated into a new warehouse and there is the potential that the local municipality will be inspecting the facility, it is a prudent to plan accordingly that a high piled storage permit will be required.
#8 Pallet Rack Damage
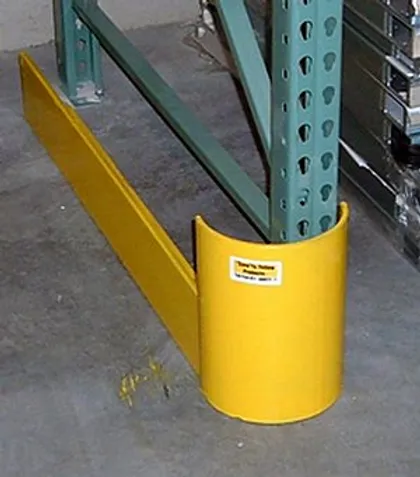
Rack damage can occur for various reasons. When the warehouse is strapped for space, tighter aisles help to increase storage space, but enhance the direct effect of forklift damage to uprights and lower beams. A common area for damage is at the end of aisles or in tunnel bays. End of aisle protectors can help to prolong the life of pallet rack in those problem areas. Column protectors can help prevent damage to the base of the upright columns commonly experienced with reach truck applications.
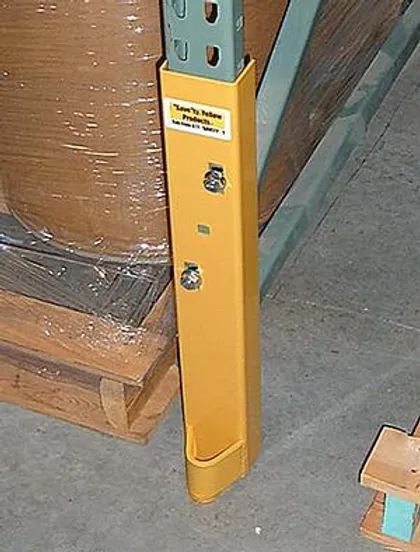
Material Handling & Storage, Inc. has been incorporated since 1992. MHS specializes in the design, integration and installation of storage systems, automated systems, pallet rack and conveyor. Our focus is on improving cube utilization and increasing productivity within manufacturing, warehousing and distribution centers.
Contact MHS to learn more on improving efficiency in your warehouse